In a previous blog post we saw how Roll-2-Roll® Sensor is not just a simple sensor but more like a vision based system that is simpler to use. Specifically we saw that they are more like a 1D line scan camera. In this blog post we will dig deeper into line scan camera technology to compare the Roll-2-Roll® Sensor technology with typical line scan cameras.
What is a line scan camera?
As the name suggests, line scan camera is a one dimensional camera with the imaging element (pixels) arranged on a single line. Unlike most cameras where the image captured is a two dimensional (2D) image, line scan cameras capture one dimensional (1D) image. A 2D image is created from a 1D image capture by either moving the camera or moving the object. Hence line scan cameras are commonly used in inspection of continuously moving objects such as inspection of a web or inspection of objects on a conveyor belt. By aligning the one-dimensional array perpendicular to the motion of the object the whole image of the object is created one line at a time. Each line is captured and integrated to form a 2D image by synchronizing the each image capture based on the speed of the moving object or the web speed (usually with an encoder).
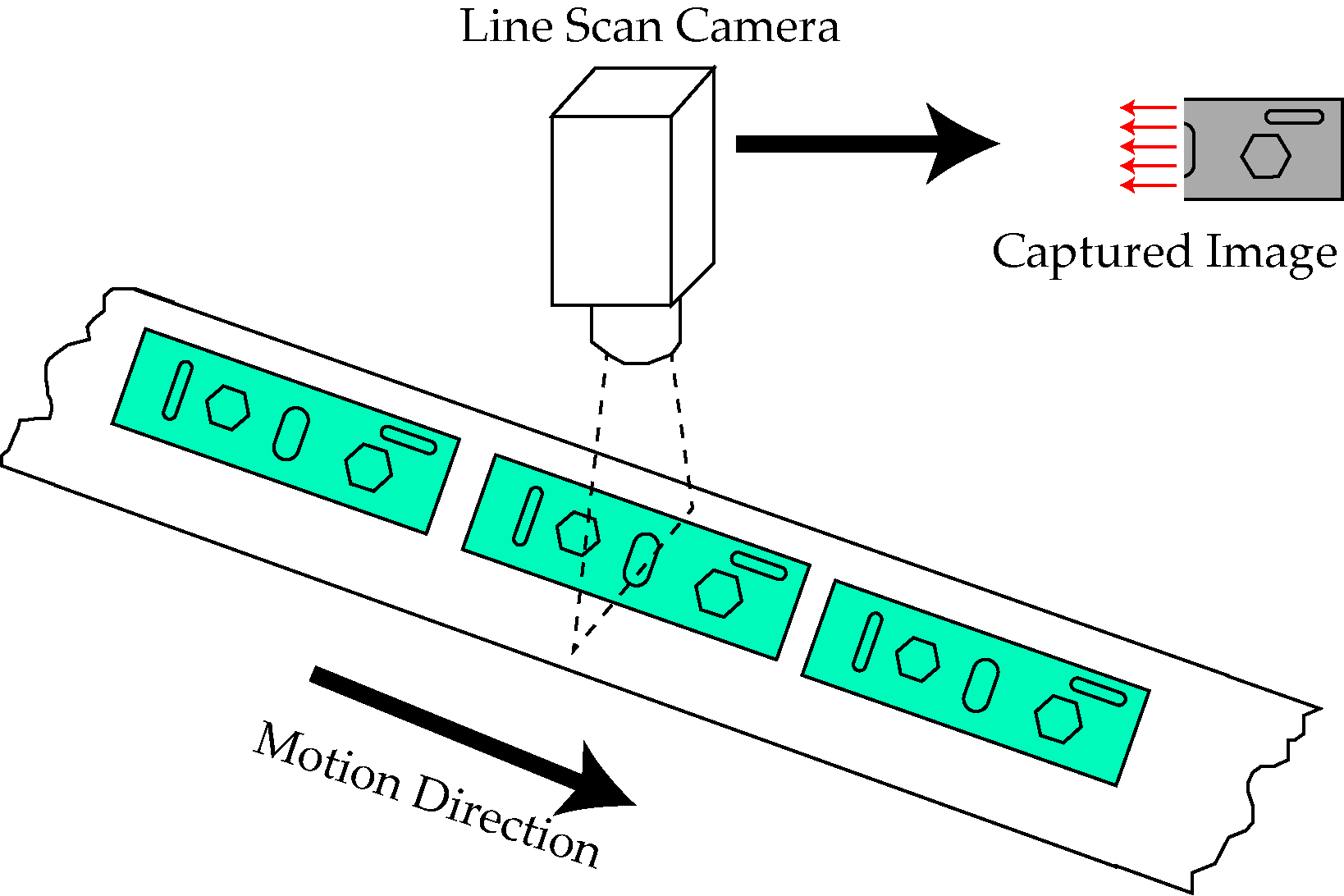
Advantages of line scan cameras for roll-to-roll inspection applications
Compared to a 2D frame camera, line scan cameras have several advantages for inspection of continuous moving objects or inspection of products on roll-to-roll machines.
- The exposure time with a 2D camera should be short (compared to the web speed) in order to capture the image without blur. Defect detection for high speed applications (over 2000 fpm or 10m/sec) are not possible with an affordable 2D frame camera. On the contrary 1D line scan cameras are extremely fast with scan rates of over 200 kHz or 5 microseconds per line enabling high speed defect detection.
- With a line scan camera the lighting for the camera can be concentrated along a line rather than a rectangular region, thereby reducing the illumination cost. Additionally, lower exposure time with a 2D frame camera requires high power external lighting adding to the overall cost.
Line scan camera types and specifications
Within line scan technology there are several different types of cameras based on the image sensor technology: CMOS (complementary metal oxide semiconductor) or CCD (charge coupled device). The image sensors also have different resolutions based on the number of pixels in the camera and the closeness of the pixels (pitch between the pixels). Common pixel counts range from 512 pixels, 1024 pixels to up to 16K pixels while the pixel pitch ranges from 5 µm (1µm = 0.000001 m = 1e-6 m) to 14 µm. Finally, the scan rate is another common specification that is important for line scan cameras with typical line scan rate of 5 kHz to 200 kHz, i.e., each line of image is captured even 200 microseconds to 5 microseconds.
Optics for the line scan cameras
The real world application requirements are translated into above specification requirements for the image sensor with a proper choice of optics or lens for the camera. Circular lens optics is the most common type of lens used by line scan cameras. Circular optical lenses enable the camera to capture an object much bigger than the camera sensors by focusing the image on the camera sensor with certain magnification (or demagnification). The focal length and magnification of the lens is chosen based on the number of pixels in the camera, the size of the object or desired field of view and the minimum feature size to be detected. And the relationship between the working distance, focal length and the magnification is as follows: working distance = (focal length) x ( 1 - (1/magnification)).
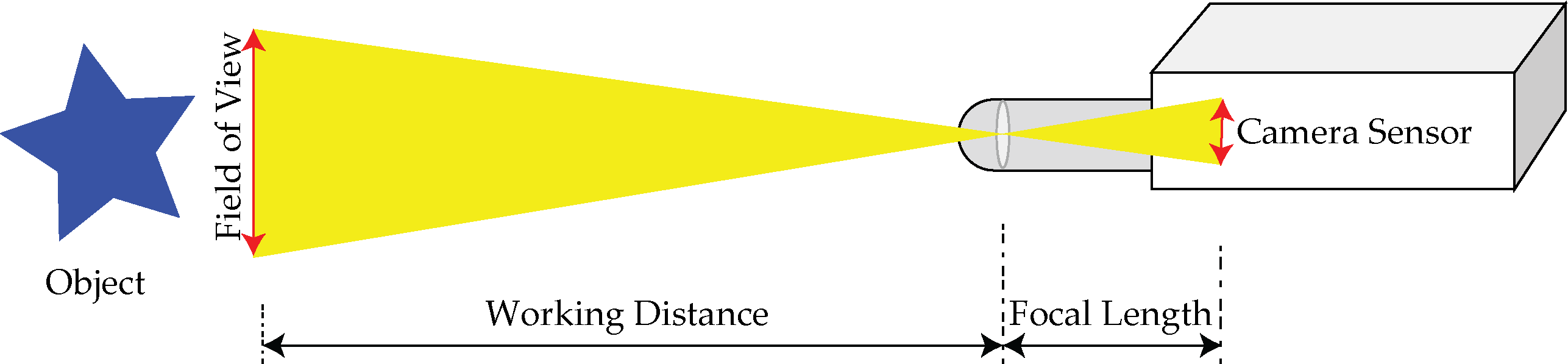
Problems with conventional optics
Smaller Pixel Size to accommodate standard lens
Circular optics, typically designed and paired with for 2D image sensors, are also used with 1D line scan cameras. Standard lens mounting option like a C-mount option is typically used with line scan cameras. More expensive lens mounts such as T-mount and F-mount are also used with higher pixel count line scan sensors. The standard mounting options not only define the maximum lens diameter but also the flange focal length.
When the pixel count increases, the overall size of each pixel is typically reduced so that standard camera mounts can be used. For example, the C-mount lens with mounting thread diameter of 1 in or 25.4 mm cannot be used with any line scan camera with line length more than 20 mm. With 2K pixels the size of the individual pixel (pitch) should be no more than 9 µm in order to use a C-mount lens. Likewise with 8K and 16K lines the pixel size has to be limited to 5 µm so that a F-mount or a T-mount lens could be used. As the pixel count increases the pixel size gets smaller to ensure that standard lens mounts can be used since medium format lenses are very expensive.
With smaller pixel size the sensitivity of the camera is reduced and this affects the overall inspection capability. Additionally, smaller pixels also require high powered external lighting to compensate for its lower camera sensitivity.
Working Distance and Object Size
When the field of view of the object to be inspected is large, then the working distance from the camera to the object is also large. This is because larger objects require larger magnification for the same focal length. When the distance between the object and the camera is large a separate gantry or special mounting system might be needed to mount the camera with respect to the object. Additionally this also necessitates free space between the camera and the object. Hence inspection of wide objects in tight installation spaces becomes difficult and would require multiple cameras to inspect the wider object.
Distortion, Lens Errors and Focus
Another main problem with circular lens optics is the distortion and lens errors. The lens aberrations and distortions can cause the image to appear larger or smaller at different radial locations of the lens. The errors are especially noticeable with smaller focal lengths. However, using larger focal lengths would also result in larger working distance and might not be possible for all installations.
The lens errors are sometimes compensated by software with calibration. However without a proper optical design and installation, the use of circular optics with line scan cameras can create errors in gauging and measurement applications.
How does the Roll-2-Roll® Sensor compare to a line scan camera
Roll-2-Roll® Sensor actually has a line scan camera with pixel counts ranging from 768 pixels (WPS 48) to 14,336 pixels (WPS 900). The main difference is in the optics; instead of circular lens optics Roll-2-Roll® Sensors use linear optics.
The optical fiber properties enable them to act as a lens that can capture light or focus an image onto the imaging element or a pixel. By adjusting the refractive index of the fibers the optical lens can be appropriately designed for image magnification. In principle multiple fibers can be arranged in a tightly packed linear array where each fiber can collect and focus light onto a single pixel as shown below. The fibers can also be staggered on multiple rows to allow a continuous image.
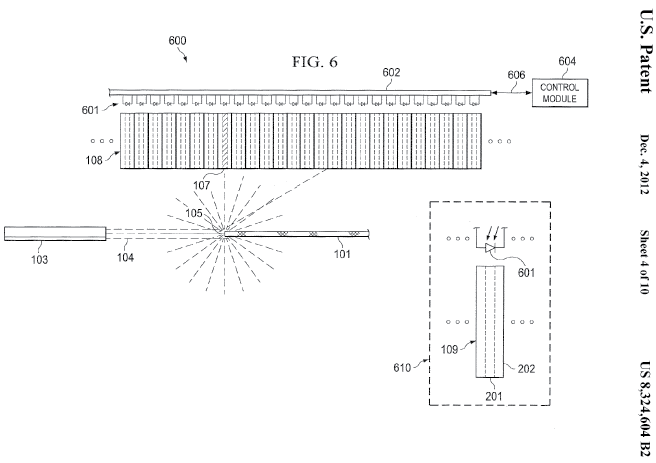
Advantages of linear lens optics for line scan cameras
Larger Pixel Size for Higher Light Sensitivity
By proper design of the refractive index of each individual lens element the linear optical array can provide an image with 1x magnification without image inversion. With 1:1 image transfer the pixel sizes can be as large as the minimum feature size of the object to be detected. In fact, a pixel can be an individual photo diode or an avalanche detector if needed by the application. For most applications, the linear optics focuses the image onto off-shelf pixel arrays with pixel sizes in the range of 63.5 µm x 63.5 µm (400 DPI) or 127 µm x 127 µm (200 DPI). These pixels are significantly larger than conventional line scan camera sensors providing over 100 times more light sensitivity. This significantly reduces the need for special high intensity lighting while having the ability to detect small contrast changes in the image.
Closer Working Distance and Compact Overall Installation
With 1x magnification afforded by the linear lens optics, the object and its corresponding image captured on the camera sensor are of the same size. So if an image of 900 mm wide needs to be captured then the camera is also 900 mm wide. The WPS 900 is such a camera with over 14,000 pixels and having an image capture range of 900 mm. With 1x magnification the working distance essentially equals the focal length of the lens. And with the focal lengths being fixed, it can be designed to be a lot smaller than with a circular lens. In fact for most of our sensors the working distance is 15 mm or less. Closer working distance also enables us to integrate the lighting with the camera. Overall requiring much less space for installation. This enables integration of the Roll-2-Roll® Sensors in tight working spaces.
Reduction of Lens Errors and Telecentric View
The linear lens because of its optical properties do not have issues with aberrations and distortion. Hence the image magnification is fixed at any point along the length of the lens. The reduction of errors enables high precision measurements without optical lens distortion. Effectively the linear lens optics behave as telecentric lenses, when the object is at the focal length, albeit being inexpensive compared to typical circular telecentric lens.
Conclusion
In conclusion, Roll-2-Roll® Sensors bring the benefit of line scan cameras along with the benefit of linear lens optics to enable a system that is affordable, compact, highly accurate and simple to use. For certain applications they are a viable cost effective alternative to traditional vision systems with 2D or line scan cameras. If you want to add simple inspection capabilities to your process Roll-2-Roll® Sensors can help with your application needs. Please contact us to know more about how we can help.